Heidenhain Millplus User Manual
Im trying to add an HR410 handwheel to my 1999 DMU50v Millplus control. Its an RS485 connection from the handwheel to the control CPU, in this case a Radisys EPC-8.
- Template.pdf - HEIDENHAIN. MillPlus IT V600.
- Heidenhain Manuals Instruction Manual and User Guide for Heidenhain. We have 81 Heidenhain manuals for free PDF download.
User Training MANUALplus 4110 NC Software 507 807-xx 9/2004. This manual is intended to improve your operation and programming of the MANUALplus 4110.
I dont have the correct handwheel adapter so Im simply trying to connect the three signal wires out of the HR410 (see wiring diagram labeled DSR TXD/ RXD/) to the RS485 COM2 port as indicated in my electrical prints. Problem is it doesn't actually show the wire connection, just the cable. Where exactly would I connect the three signal wires green, yellow, grey, from the HR410 to on the COM2 pictured? Ive looked online and three wire RS485 connections are standard but I cant tell exactly how I should connect to this particular EPC-8 port. Yes, I tried DMG and heidenhain. No techs at either place claim to know how the HR410 is supposed to connect to a serial port, even though its the most common handwheel for both???
The Heidenhain tech indicated that a serial connection must take place before the handwheel will show any sign of being activated. So even if its powered up on the brown and white wires with 12vdc, it wont show any activity, LEDs, estop, etc (it does not). If anyone knows RS485 and has any suggestions it would be much appreciated! Here's a problem, the HR410 handwheel is neither RS422 or RS485, it's RS232, because it doesn't have differential signalling. The board the HR410 attaches to has TXD+/RXD+ and TXD-/RXD- signals that go to the control. This an RS232 to RS422 converter board. In RS232, TXD goes to RXD, RXD goes to TXD, and DSR goes to DTR; RTS connects to CTS and vice-versa.
In this case, the HR410 connects to the RS422 adapter board, which turns the TXD/ signal line into a differential TXD+/TXD- and the RXD/ signal line into an RXD+/RXD- line. The DSR should pass through and connect to the DTR line. I suspect the DSR is used to enable the handwheel to send data to the control, since the control has 2 devices shown on the RS422/485 bus. It's possible that they implemented an inverter to select either the mini-PC or the handwheel, DTR low mini-PC, DTR high handwheel, or somesuch. You will need to experiment and see if it works with DSR to DTR or if you need an inverter to select the handwheel.
I think you're on the right path here. The answer to this: 'So TD(a) on the adapter RS485 pins is the same as TXD+?
TD(b) is TXD-? Same with RXD?'
And you don't even have to get the polarity correct, although it helps. But if you make it thru the screed below, the e-stop and approval switch data has to already be on the line. Your adaptor may not work as a direct substitute for board 19a4, if you're also trying not to have 19a3, for example. Also, double check that it supports all the control lines. Doesn't look like there are enough connectors to make that happen. Text wall commences: 232 is 'single ended'.
One wire for transmit, one for receive, referenced to ground. 422 is balanced/differential - a + and - for transmit, +, - for receive, not referenced to ground, and capable of 4000 feet, instead of 50 or so for 232.
Both the above are for point - to - point use, as in computer to peripheral. (But hardware flow control is available.) 485 is electrically like 422, but it has an addressing protocol that can be used to communicate with one of several devices on the same circuit. This requires that the controlling computer knows who to call, and the peripheral knows to answer. So if your machine has various things that plug into that 485 circuit, the devices and the controller will have a specific protocol, which won't be only hardware, but will require the hardware hooked up correctly to work. 19a1 is labeled like a 422/485 port, but the connection to the mini-pc is clearly 232.
The same y-cable connects to. 19a4 X4 as 422/485, with balanced/differential signal and control lines. Now, you can, in a pinch, do a kluge conversion between 232 and 422 by just using the + signal of the 422 referenced to ground, but it kills the benefits of 422. Maybe they do it because mini-pc is always local to the machine, and disconnected except for loading?
Or maybe that's not a y-cable, but just optional connections. The signals that go between 19a4 X8 and 19a3 X1 seem to be back in 232 land, and calling for your handwheel to be 232, not 422/485 as mentioned above.
Network simulation opnet guide. • Used in hands-free headsets and car kits. • Wireless synchronization.
That means 19a4 is acting as a 232/422 converter, and E-stop interface (to inject e-stop and approval switch status info into a serial data stream.) I wonder if the mini-pc and the handwheel are mutually exclusive options? Or at least not intended to be active simultaneously? They seem to imply local and remote handwheels, too, based on drawing notes. Maybe the local one is 232, and the remote is 422/485.If you're trying to use a generic converter for 19a4, it won't have the e-stop and approval switch information on the data line, and the CPU may not run the program if it thinks e-stop is triggered. (And good design would require absence of e-stop info (in a data line where it's expected) would mean that e-stop is triggered.) You can use a program called RealTerm (free) that will let you investigate what all this stuff is doing, if you have to dig into it.
You'll need a 422/485 to (probably) USB adaptor that supports all data signalling lines in order to fully scope things out. But it will also tell you if your handwheel is working, and if the other ports are working as well. I'm glad I get to be outside today.
Heidenhain Cnc
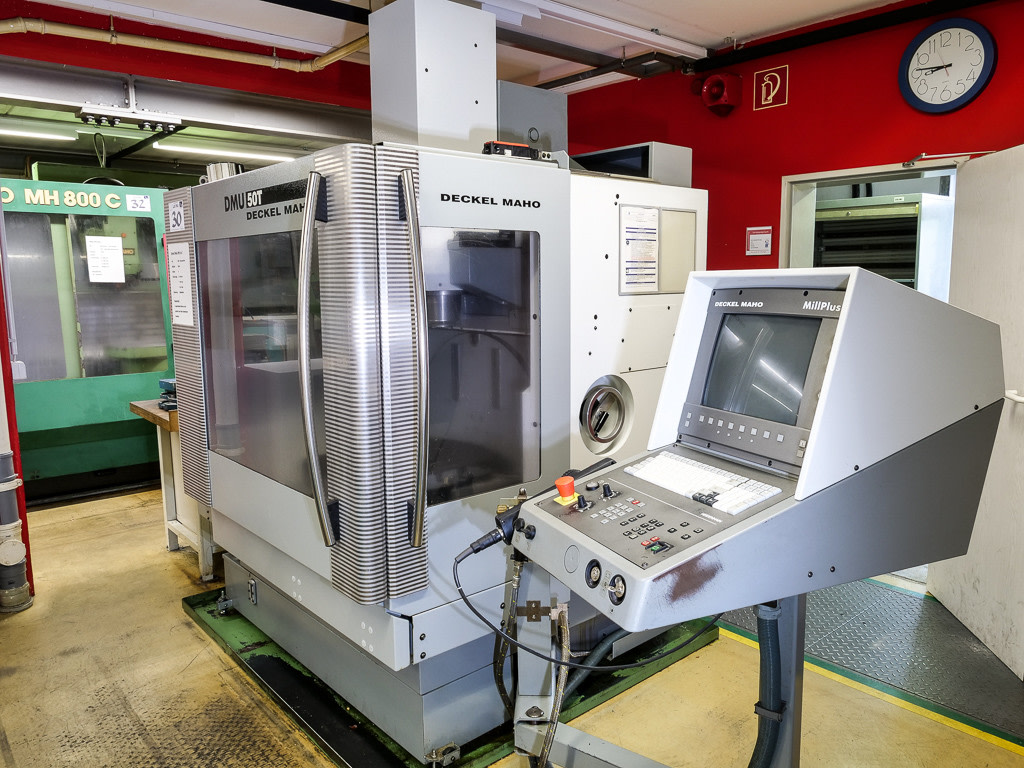

Picked up an ADAM 4522 RS232 - RS422/485 adapter. Wired it as indicated in the wiring as an RS422 connection to COM2. Control does not see the HR410. Oh well, I ordered the correct(expensive) adapter from DMG. My electronics guy thinks there is more than just a simple RS232-RS422 converter in the adapter maybe some electronics that are required to initiate a connection. This is the Philips 1220 VME version of the Millplus hardware, a bump in the road towards migrating to all heidenhain controls.
The previous verions of Millplus. After getting passed around at DMG for awhile, I finally found a guy who knew about the RS232 to RS422 adapter for my machine.
I ordered one from DMG and now the control sees that there is a handwheel attached. If no HR410 handwheel is connected, (even if the 19A4 serial adapter thingy is attached, the 'handwheel' selection in the MDI pull down menu will appear. In MDI mode I can select 'handwheel 1' and select the axes, which green lights the right numeral in the axis window on rhw MDI page. If a handwheel is attached, the 'handwheel' selection in the MDI pull down menu does not appear, thats because now its supposed to be selected using the permission buttons on the handwheel. But that doesnt actually work, the control 'sees' the handwheel but will not activate it.
Cnc Flow Control
Looks like I need to wire the two barrier blocks for estop and permission on the adapter, to my machine. Problem is my wiring diagram does not show the handwheel wiring as it didnt come with that option installed.
Heidenhain Millplus User Manual
It just shows the permission barrier block, and the estop barrier block hanging there unconnected. No one at DMG seems to know for certain how to connect these or even if they need to be connected. Does anyone out there have a DMG machine with Millplus and a HR410 that could either take a photo of the wiring in the operator station, or send me your wiring page showing the HR410 Estop/permission wiring? Much appreciated.